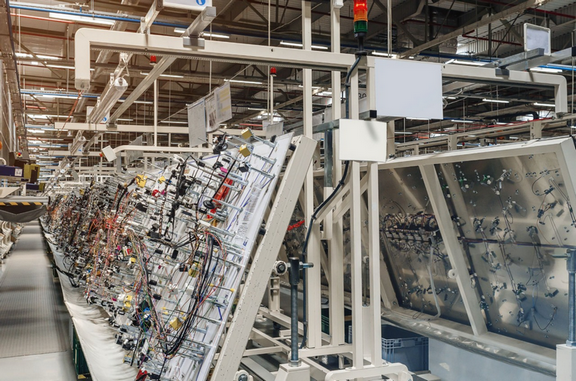
Build Harsh Environment Wiring Harnesses: Top Rugged Designs
Introduction
In mission-critical applications where failure is not an option—from EV powertrains and aerospace systems to industrial automation and defense-grade electronics—harsh environment wiring harnesses are a foundational necessity. At Celestix Industries, we specialize in designing and manufacturing custom harsh harness designs that withstand the extreme: high heat, vibration, chemical exposure, moisture ingress, and electrical interference.
With over a decade of expertise and a legacy of reliability, we engineer wiring harnesses for harsh conditions that not only meet but exceed the most stringent industry requirements. Our capabilities extend from concept to production, enabling us to solve the most complex challenges across sectors with rugged harness design.
We serve customers who cannot afford downtime. In these markets, the extreme condition wire harness isn't just a commodity—it's a backbone of system reliability, safety, and compliance, making Celestix a trusted rugged harness supplier.
Key Challenges in Harsh Environments
Designing wire harnesses for rugged applications involves engineering durable harness solutions that endure the following:
Thermal Stress
Heat-resistant wiring harnesses may be subjected to temperature ranges from -60°C to +260°C depending on the application.
Aerospace and engine bay environments demand materials that maintain electrical integrity and mechanical flexibility across wide temperature swings.
Thermal expansion and contraction must be considered in harsh environment harness design to avoid mechanical strain on connectors and joints.
Materials must resist degradation over time under continuous high-temperature conditions—a leading cause of insulation cracking and short circuits.
Vibration and Mechanical Fatigue
High-frequency and multi-directional vibration in EV drivetrains, construction machinery, or aircraft can degrade wires and connectors in vibration-resistant harnesses.
Long-term exposure can cause fretting corrosion at contact interfaces.
Dynamic motion introduces flex fatigue—especially in robotic arms and suspension systems—where flexible rugged harnesses excel.
Strain reliefs, grommets, vibration-dampening over-molding, and strategically placed clips prevent micro-movements that cause long-term failures in high-performance harsh harnesses.
Moisture, Dust, and Chemical Resistance
IP67/IP69K sealing is vital for weather-resistant harness designs in marine, off-road, and industrial applications where exposure to water, oil, and solvents is frequent.
Corrosion-resistant wire harnesses must resist long-term exposure to chemicals like hydraulic fluid, coolant, and degreasers.
Salt spray and condensation create corrosive environments requiring anti-corrosive coatings or materials, critical for marine wiring harness design.
Materials are tested against ASTM D543 and ISO 1817 for chemical compatibility.
EMI/RFI Shielding
Signal integrity is compromised in environments with high electromagnetic interference, addressed by shielded harnesses for harsh environments.
Shielded cables and connectors with multi-layer braided designs are used to suppress noise and maintain data fidelity.
Grounding strategies and differential signal pair design are employed for improved performance in aerospace harnesses for harsh conditions.
EMI mitigation is not optional in defense, aerospace, and autonomous vehicle applications where miscommunication can be catastrophic.
Material Science Behind Reliable Harnesses
Reliability in harsh conditions begins with meticulous material selection and validation for reliable harnesses in harsh conditions:
Conductors
Tinned copper offers enhanced corrosion resistance and is standard for marine wiring harness design and outdoor use.
Silver-plated copper is favored in high-frequency and aerospace harness harsh conditions due to superior conductivity.
Aluminum-copper hybrids reduce weight while maintaining current capacity, ideal for automotive harsh harness design in EVs.
Nickel-plated copper is used in high-temperature military rugged harness environments.
Selection depends on ampacity requirements, environmental conditions, and installation constraints.
Insulation
PTFE: Operates from -200°C to +260°C, excellent chemical resistance for extreme condition wire harnesses.
Silicone: High flexibility and heat resistance, widely used in medical and automotive harsh harness design.
XLPE and TPE: Tough, thermally stable, and abrasion-resistant for durable harness solutions.
FEP, ETFE, and PFA: For extreme environments requiring chemical, heat, and flame resistance in mining harness design.
Insulation is selected not just for durability but also for signal attenuation, outgassing, and flame retardance.
Sheathing & Protection
Braided sleeving (glass wool or polyester): Adds abrasion and rodent resistance with protective sleeving harnesses.
Corrugated tubing and LSZH jackets: Improve fire safety and are suitable for confined or populated spaces in industrial rugged wiring harnesses.
Over-molding with TPU/PBT/nylon: Delivers vibration dampening, strain relief, and ingress protection for compact durable harnesses.
Heat shrink tubing with adhesive lining: Provides sealing and strain relief in high-stress areas.
Choices are validated through ASTM D4060 (abrasion), UL 94 (flammability), and DIN EN 60512 (durability).
Engineering Standards and Testing Protocols
At Celestix, quality is engineered in. Every Celestix harsh harness design is built and tested under:
Standards and Certifications
IPC harness design standards (IPC/WHMA-A-620 Class 3), ISO 9001:2015, IATF 16949:2016, ISO 14001, RoHS harsh environment harness, REACH
Compliance with IEC 60228, ISO 6722, and UL-approved rugged harness standards ensures international reliability.
Industry-specific standards: AS9100 (aerospace), ISO 13485 (medical), and MIL-spec harness design.
Our certification stack covers every phase of production and every environmental regulation relevant to harsh conditions.
In-House Validation and Testing
Environmental Chambers: Simulate thermal cycling, humidity, and salt spray (e.g., ISO 16750-4 conditions) for in-house rugged harness testing.
Electrical Testing: Hipot (up to 3000V), insulation resistance (>100 MΩ), and contact resistance (<10 mΩ).
Mechanical Testing: Tensile strength, flex life (10,000+ cycles), and vibration durability.
Fatigue Testing: Up to 50,000 motion cycles to simulate real-world stress in scalable harsh environment harnesses.
Ingress Protection Testing: Submersion, jet spray, and dust ingress validation for IP67/IP69K ratings.
Crimp Quality: Profile analysis using cross-section imaging and pull force measurements to ensure mechanical and electrical integrity.
Applications Across Industries
Our rugged harness designs are tailored to meet the needs of various critical sectors:
Electric Vehicles (EVs)
High-voltage (up to 1000V), shielded harnesses for harsh environments for powertrain and BMS.
Over-molded connectors for thermal and vibration resilience in automotive harsh harness design.
Designs support regenerative braking, battery charging, and safety interlocks.
Support for liquid-cooled battery modules, active thermal management, and CANbus communication in renewable energy harsh harnesses.
Aerospace and Defense
Lightweight, flame-retardant harnesses using silver/nickel-plated copper and PTFE insulation for military rugged harnesses.
Compliant with MIL-STD-810, AS9100, and IP68/IP69K ratings.
Used in avionics, drone navigation, and radar systems.
Integration with modular avionics and embedded systems requiring extreme signal fidelity.
Industrial Automation
Robust harnesses with multi-branch layouts and oil-resistant jackets for industrial rugged wiring harnesses.
Integrated sensors, actuators, and custom bus connections.
Suitable for robotics, CNC machinery, and PLC-based control panels in mining harness design.
Engineered for rapid deployment, modular replacement, and fault-tolerant control.
Medical Devices
Biocompatible and sterile-ready wiring for imaging, diagnostic, and life support equipment.
Non-toxic, low-outgassing materials suitable for clean room and patient-adjacent environments.
Customized solutions for dental units, MRI-compatible cables, and operating theater instruments.
All harnesses validated to ISO 10993 and IEC 60601-1 for medical safety compliance.
Why Celestix? Engineering Beyond Compliance
Partnership Approach
We offer CAD modeling, 3D prototyping, and joint design reviews to optimize form, fit, and function for prototype rugged harness design.
Our engineering team collaborates directly with R&D teams to ensure specifications align with field conditions for OEM harsh environment harnesses.
Design reviews are augmented with simulation testing (thermal maps, EMI susceptibility, FEA for strain distribution).
End-to-End Capabilities
Full vertical integration: wire drawing, extrusion, assembly, over-molding, testing, and packaging—all under one roof for in-house rugged harness production.
Real-time ERP integration for traceability and agile order tracking.
BOM and revision control systems linked to QA to avoid any build errors in production.
Rapid Prototyping
From initial drawings to tested samples in under 2 weeks, reducing time-to-market for prototype rugged harness design.
Prototypes are validated through simulation and field-mimicking test environments.
Quick-turnaround pilot runs allow for fast scaling and compliance documentation.
Scalability with Zero Compromise
Whether it's low-volume precision runs or high-volume automotive schedules, we maintain quality consistency with 100% in-process checks for scalable harsh environment harnesses.
Production shifts can scale 3x to meet urgent ramp-ups, backed by strategic supplier inventory.
Forecast-based capacity planning and buffer inventory for mission-critical programs.
Conclusion
Performance under pressure is not optional—it’s mission-critical. At Celestix, our harsh environment wiring harnesses are engineered with deep technical rigor, built with premium materials, and validated to global standards. We don't just supply harnesses; we deliver reliable harnesses for harsh conditions where it matters most.
Our design ethos is centered on predictive reliability, robust engineering, and long-term operational stability. As industries advance toward smarter, safer, and more demanding technologies, our role as a trusted rugged harness supplier in custom harsh harness design grows ever more vital.
Harsh environments demand excellence—not excuses. Trust Celestix to power your toughest applications with durable harness solutions.
Ready to engineer resilience into your systems? Reach out through our contact form or email to start a tailored consultation.