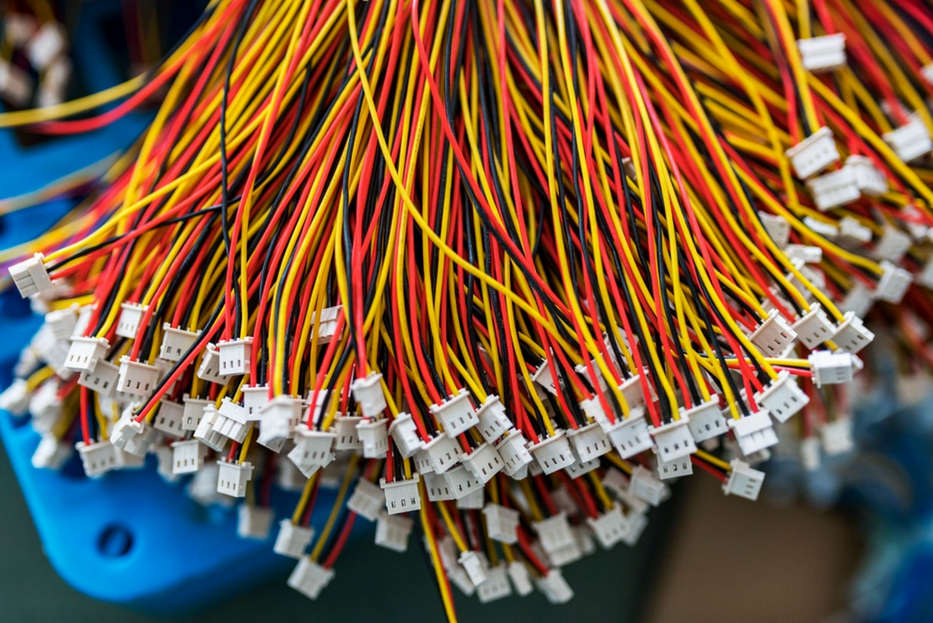
How to Test and Validate a Wiring Harness
Why Testing Matters
In custom wire harness manufacturing, testing is not optional but essential. Whether powering a smart refrigerator, a robotic assembly line, or an electric vehicle, the wiring harness is the foundation of safe, reliable performance. At Celestix Industries India Pvt Ltd, we recognize the stakes. That’s why every harness we manufacture undergoes 100% inspection, guided by industry-best standards and tailored testing procedures.
From electrical continuity to environmental resilience, our validation process is engineered to meet your specifications and exceed expectations. Our reputation as a trusted wiring harness manufacturer is built on this commitment.
Beyond functionality, testing ensures long-term durability and compliance with regulatory and OEM-specific standards. Whether it's EMI resistance for telecom applications, biocompatibility for medical devices, or fast-charging compatibility for electric vehicles, testing converts design into dependable reality.
This is the essence of wiring harness testing—ensuring your product performs consistently and safely in real-world conditions. When your project requires validated performance, Celestix delivers.
Our End-to-End Testing & Validation Protocols
We follow a rigorous test process to confirm electrical integrity, mechanical strength, and environmental durability. This comprehensive wire harness validation guide is your roadmap to reliability.
1. Continuity Testing
Purpose: Confirms complete, uninterrupted electrical pathways
Equipment: CAMI Research CableEye, in-line testers
Detects open circuits, short circuits, and miswiring
Real-time diagnostics for efficient quality control
Standard: IPC/WHMA-A-620 Class 3
Validates schematic integrity and detects wiring errors before they reach production
2. High-Voltage (Hi-Pot) Testing
Purpose: Verifies insulation performance under electrical stress
Voltage Range: Up to 5,000V AC/DC, depending on application
Simulates high-voltage stress to ensure no dielectric failure
Detects insulation breakdown that may not appear during normal use
Mandatory for all high-voltage EV harnesses and aerospace builds
Compliant with UL, IEC 60228, and ISO 6722 standards
3. Pull-Force Testing
Purpose: Evaluates mechanical strength of crimped and connected joints
Unit of Measure: Newtons (N)
Validates secure terminal crimps and ensures no dislodgement under stress
Key to verifying strain relief in dynamic environments such as automotive or machinery
Every crimp is validated to exceed customer-specific force thresholds
4. Crimp Cross-Section Analysis
Purpose: Microscopic verification of crimp quality
Tools: Precision sectioning tools, microscopy, digital analyzers
Ensures proper material deformation for low resistance contact
Identifies voids, bird-caging, or insufficient crimp depth
Analysis is logged for traceability and included in PPAP submissions
Conducted after each tooling setup or any tooling anomaly
5. Environmental Stress Testing (When Required)
Thermal Cycling: Validated between -40°C and +125°C to simulate seasonal extremes
Salt Fog and Humidity: Corrosion resistance for marine and coastal applications
Vibration Testing: In accordance with IEC 60068, replicating real-world motion stress
Abrasion Resistance: Verifies jacket and sleeve integrity under physical wear
Ingress Protection (IP): Tested up to IP67/IP68 for sealed over-molded connectors
Environmental harness testing is particularly critical for defense, renewable energy, and high-durability machinery applications.
6. Visual and Label Inspection
Purpose: Verifies visual conformity and traceability
Conducted By: IPC-certified inspectors
Confirms connector orientation, pinouts, label positioning, and color coding
Barcode checks for traceability across production batches
Ensures aesthetic quality as well as correct component integration
First-pass visual inspection is followed by secondary QA sign-off
7. Functional Testing (Customer-Specific)
Signal Integrity: Measured across data lines, CAN bus, or sensor interfaces
Connector Fitment: Measured insertion and retention force values using test fixtures
Live System Simulation: Harness integration into mock control panels for operational checks
Simulation setups mirror final field application environments, improving test relevance
Functional harness validation ensures system-level performance and interface compatibility, especially critical in applications involving multiple control modules or third-party components.
Tooling and Automation
To ensure consistent and reliable outcomes, Celestix invests in high-end testing infrastructure:
Multimeters for continuity diagnostics
Hi-pot testers for insulation breakdown checks
Automated test platforms with report generation
Custom-configured wire harness test benches
In-house test jig development tailored to customer drawings
Automation accelerates testing throughput while eliminating human error in repetitive validations. Our digital logging system also ensures complete test traceability for audits and compliance.
Specialized Testing for Key Industries
We provide tailored validation for high-performance sectors:
Automotive harness testing for thermal, vibration, and EMI resilience
EV wiring harness validation focused on high-voltage safety and fast-charging efficiency
Aerospace harness validation using lightweight materials and IP-rated components
Appliance harness testing for energy efficiency and moisture resistance
Industrial harness test guides for control panels, PLCs, and robotics environments
We support full PPAP packages, First Article submissions, and Engineering Change control. Our validation programs are customizable for end-product requirements, launch timelines, and regional certifications.
Certifications That Set Us Apart
Celestix’s quality control is aligned with global and regional standards:
ISO 9001:2015, IATF 16949:2016, ISO 45001:2018
UL, CE, RoHS, REACH, ISO 14001
BIS-compliant testing for Indian regulatory requirements
IPC/WHMA-A-620, J-STD-001 testing standards
We ensure compliance documentation, test logs, and material declarations are available for every shipment.
What You Receive with Every Shipment
Every Celestix harness includes a robust documentation and validation package:
Certificate of Conformance (COC)
Full continuity, high-voltage, and mechanical test records
Material safety and RoHS/REACH compliance statements
Product labeling and traceability reports
CAD drawings or wiring diagrams upon request
All testing data can be archived electronically or integrated into your QA system.
Why Choose Celestix for Harness Validation
Every conductor, terminal, and crimp point is verified to the highest standard. At Celestix, testing is not a checkpoint—it’s a philosophy. We combine extensive engineering knowledge with precision validation systems to deliver products that are truly production-ready.
Your application demands more than functionality—it demands assurance. From high-voltage reliability to EMI protection and environmental resilience, we engineer certainty into every wire harness.
To begin your next validated wiring project, fill out our contact form or email the Celestix team today.
Ensure Performance. Prove Reliability. Deliver with Confidence.