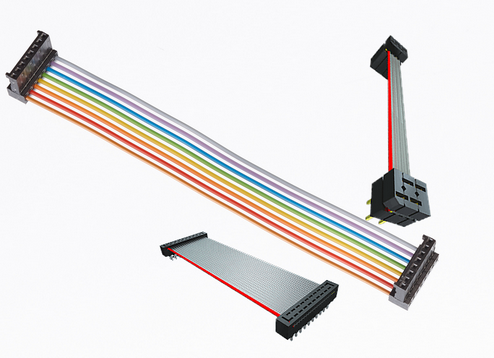
IDC Cable Assembly: Technical and Commercial Comparison with Other Cable Assemblies
Insulation Displacement Connector (IDC) cable assemblies are widely used in electronics, telecommunications, and industrial applications due to their efficiency in mass production and reliable electrical connections. However, they differ significantly from other types of cable assemblies such as crimped, soldered, or standard wire harness assemblies. This article explores IDC cable assemblies in-depth, comparing them with alternative solutions from both technical and commercial perspectives.What is an IDC Cable Assembly?
An IDC (Insulation Displacement Connector) Cable Assembly is a type of electrical connection where the connector is designed to cut through the insulation of a wire to establish a secure connection without requiring stripping or soldering. These assemblies are commonly used with ribbon cables in applications such as:
- Consumer electronics
- Telecommunications & data networking
- Industrial automation
- Medical devices
- Automotive electronics
Key Features of IDC Cable Assemblies:
- No need for wire stripping or soldering
- Fast and reliable mass termination
- Cost-effective for high-volume applications
- Low electrical resistance connection
- Available in multi-conductor configurations (typically used with ribbon cables)
Technical Comparison: IDC vs. Other Cable Assemblies
1. IDC vs. Crimped Cable Assemblies
Feature | IDC Cable Assembly | Crimped Cable Assembly |
---|---|---|
Connection Method | Uses insulation displacement, cutting through insulation to make contact | Requires stripping the wire and attaching a crimped terminal |
Ease of Assembly | Fast, one-step termination process | Requires manual or automated crimping, increasing processing time |
Durability & Reliability | Good for vibration-resistant applications, but may not be as strong as crimped | Very strong mechanical connection, ideal for automotive and industrial applications |
Conductivity & Resistance | Low resistance connection | Similar or better, depending on crimp quality |
Wire Compatibility | Mostly used with ribbon cables | Works with a variety of wire types and sizes |
Common Applications | Electronics, data cables, low-power signals | Automotive, power cables, industrial applications |
Verdict: Crimped connections are more versatile and durable for rugged environments, whereas IDC is better suited for quick, cost-effective, high-volume applications.
2. IDC vs. Soldered Cable Assemblies
Feature | IDC Cable Assembly | Soldered Cable Assembly |
---|---|---|
Connection Method | Uses insulation displacement | Soldering wire directly to terminals or PCB |
Ease of Assembly | Quick, one-step process | Requires skill, time, and additional materials (solder, flux) |
Durability | Good for flexible and vibration-resistant connections | Highly reliable for permanent connections |
Conductivity & Resistance | Consistently low resistance | Can achieve even lower resistance but is more prone to oxidation |
Wire Compatibility | Best for ribbon cables | Works with various wires, including multi-core shielded cables |
Common Applications | Consumer electronics, data transmission | High-end electronics, aerospace, military applications |
Verdict: Soldered connections are ideal for high-reliability applications, but IDC provides a faster, mass-production-friendly alternative.
3. IDC vs. Standard Wire Harness Assemblies
Feature | IDC Cable Assembly | Standard Wire Harness |
---|---|---|
Connection Method | Mass termination via insulation displacement | Uses a variety of connections (crimp, solder, screw terminals) |
Ease of Assembly | Automated, very quick | Requires manual routing and connection |
Flexibility | Limited to flat ribbon cables | Can include multiple wire types, different gauges, and configurations |
Durability & Protection | Less protected from external damage | Often includes protective sheathing, braided shielding |
Cost | Lower per unit for mass production | Higher due to manual labor and customization |
Common Applications | Consumer electronics, telecommunications | Industrial automation, automotive, aerospace |
Verdict: Standard wire harnesses offer more flexibility for custom applications, while IDC is best for mass-produced, compact solutions.
Commercial Comparison: Cost, Scalability, and Suitability
Factor | IDC Cable Assembly | Other Cable Assemblies |
---|---|---|
Manufacturing Cost | Lower for mass production | Higher due to labor and materials |
Scalability | Highly scalable | Requires more effort to scale |
Customization | Limited (designed for ribbon cables) | Highly customizable |
Reliability in Harsh Environments | Moderate | High (especially crimped and soldered assemblies) |
Time to Market | Faster due to automation | Slower due to manual assembly |
Key Commercial Takeaways:
- IDC assemblies are cost-effective for high-volume production.
- Crimped and soldered assemblies provide more durability and are preferred for automotive and industrial applications.
- Standard wire harnesses are ideal when customization and robustness are required.
When to Choose IDC Cable Assemblies
IDC cable assemblies are best suited for:
- Mass-production electronics (computers, printers, networking devices)
- Low-power signal transmission (telecommunications, data cables)
- Consumer appliances (washing machines, televisions)
- Automotive low-voltage applications (infotainment systems, dashboard controls)
When to Avoid IDC Cable Assemblies
- High-power applications (Battery and power cables in EVs)
- Extreme environments (high vibration, temperature fluctuations)
- Custom or flexible wiring needs (industrial automation, aerospace, medical)
Conclusion
IDC cable assemblies provide a fast, cost-effective, and reliable solution for specific applications, particularly in consumer electronics and telecommunications. However, for high-durability and high-power applications, crimped, soldered, or standard wire harnesses offer superior performance.
Choosing the right cable assembly depends on application requirements, volume, cost constraints, and durability needs. Celestix Industries can provide custom IDC, crimped, soldered, and over-molded cable assemblies tailored to your industry needs.
For expert consultation on selecting the right cable assembly, contact Celestix Industries today.