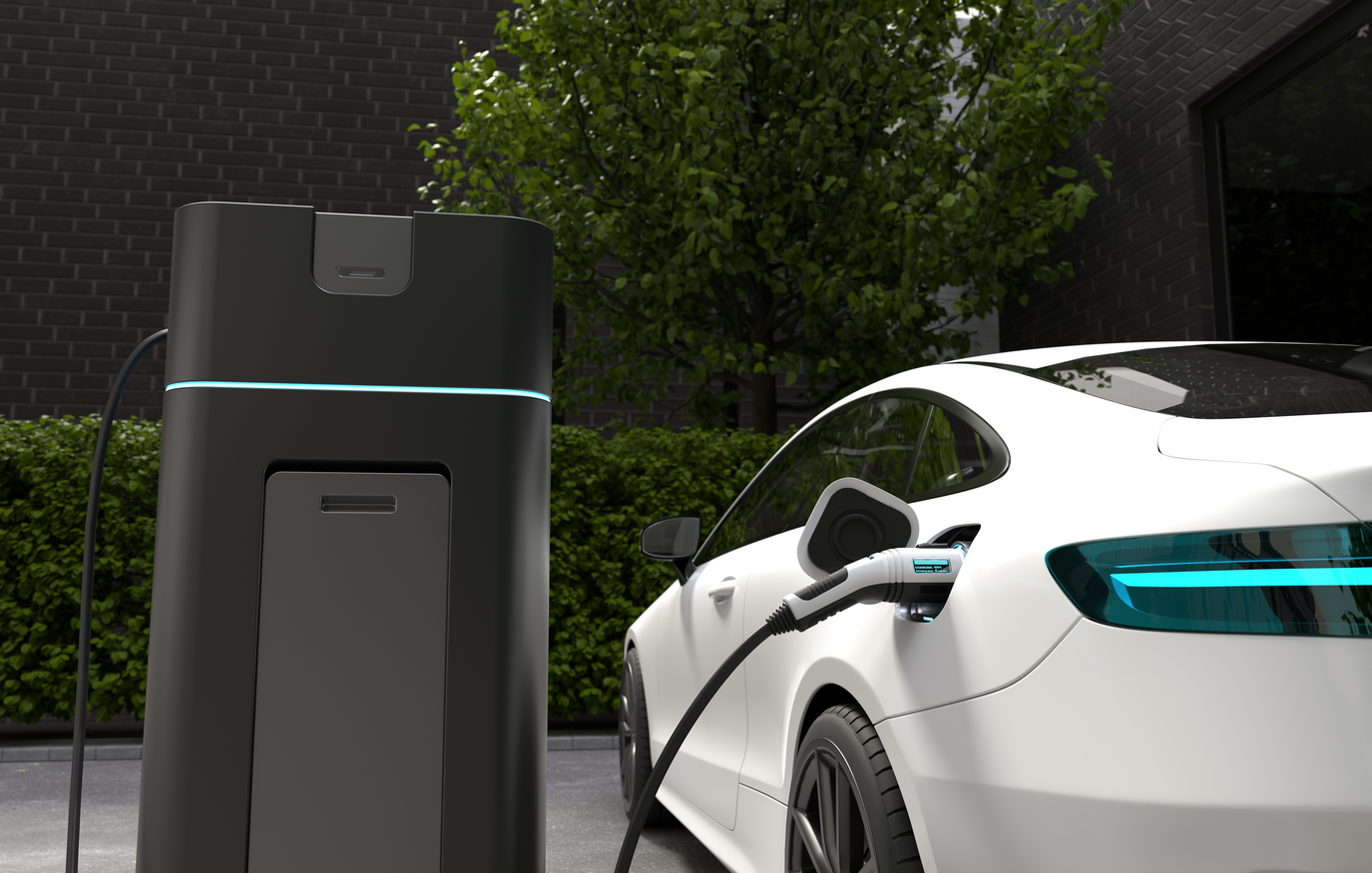
Wiring Harnesses in Electric Vehicles: Challenges and Solutions
Electric vehicles (EVs) are redefining performance, sustainability, and smart mobility. At the core of every EV, high-voltage wiring harnesses play a critical role in safely routing power and data signals. As a trusted EV harness manufacturer specializing in custom wire harnesses, Celestix Industries India Pvt Ltd delivers expertly engineered solutions to meet the evolving demands of modern EV platforms.
Our offerings address not only the well-known complexities of EV wiring harness design, thermal management, and electromagnetic interference, but also growing expectations around sustainability, automation, and long-term reliability.
Core Challenges in EV Wiring Harness Design
1. Managing High Voltage Loads
Modern EVs operate at 400V to 800V—and even up to 1000V in advanced platforms. These high voltages require advanced harness designs featuring superior insulation, reliable connectors, and effective thermal management. Without the right engineering, issues can include:
Voltage drop under dynamic loads
Overheating and insulation breakdown
Shortened battery life and reduced efficiency
Celestix specializes in high-voltage EV harness systems that deliver safety, durability, and performance.
2. Controlling EMI and Signal Interference
Electric vehicles incorporate numerous electronics, including motor controllers, BMS, infotainment systems, and autonomous sensors. These systems must communicate reliably. Inadequate EMI/RFI shielding can cause:
Signal degradation and sensor errors
Interference with ADAS systems
Reliability issues and fault alerts
Our shielded EV wiring harness solutions protect sensitive signals and meet stringent international standards.
3. Minimizing Weight
Heavy wiring increases energy demand and reduces EV range. Traditional copper-heavy designs are no longer optimal. Effective EV harness weight reduction requires:
Switching to aluminum EV harness wiring or hybrid conductors
Minimizing redundant circuits
Merging functional branches into unified systems
We deliver lightweight EV harnesses that maintain mechanical and electrical integrity.
4. Navigating Space Constraints
Tight under-hood and underbody spaces, combined with thermal and mechanical challenges, complicate harness routing. EVs require:
Small bend radii
Strong strain relief
Thermal insulation and abrasion resistance
Celestix addresses EV wiring harness complexity with modular EV harness design options that optimize layout and assembly.
5. Enabling Fast Charging
Fast-charging demands significant current over short durations. Without engineered harnesses, this can result in:
Heat buildup
Safety risks
Slower charging speeds
We develop advanced harnesses for EV charging harness design, capable of supporting up to 500A.
6. Resolving Supply Chain & Production Challenges
In a rapidly scaling market, component shortages and logistical inefficiencies can delay production. We mitigate these issues by offering:
Robust EV harness supply chain management
Strategic VMI programs
In-house EV wiring harness production capabilities
7. Ensuring Durability in Harsh Conditions
EV harnesses must endure heat, moisture, vibration, and chemicals. Celestix’s designs focus on:
Moisture protection and anti-corrosion treatments
Flexible, vibration-resistant assemblies
IP67/IP69K-rated connectors and over-molding for harsh environments
How Celestix Delivers Advanced EV Harness Solutions
We provide complete wiring harness solutions for electric vehicles, combining precision engineering, comprehensive testing, and strict adherence to international certifications.
High-Voltage and Thermal Management
Our flame-retardant over-molding technology, certified to UL 94V-0 standards, enhances safety in high-heat environments by protecting internal conductors from exposure to extreme temperatures and electrical faults.
We utilize heat-resistant insulation materials including Silicone, Teflon, and XLPE, enabling our harnesses to withstand continuous operation in high-voltage systems without degradation.
Each design is customized to meet the unique thermal and spatial demands of battery systems, addressing EV battery harness challenges with optimized routing for improved heat dissipation.
EMI Shielding and Signal Integrity
We implement advanced shielding techniques, such as layered braided and foil combinations, with precision-grounding strategies to mitigate noise and preserve data integrity.
Our harnesses are fully compliant with ISO 11452, CISPR 25, and ADAS-level EMC standards to ensure reliable operation in electronically dense EV environments.
Lightweight and Space-Efficient Design
We deploy flat cable configurations and low-profile molded junctions that minimize the harness footprint while maintaining performance and reliability.
Each harness is meticulously routed using CAD-driven layouts to optimize bend radii, reduce bulk, and enable easy integration into compact vehicle spaces.
Charging Performance and Power Integrity
We use high-conductivity, low-resistance conductors to reduce power loss and heat generation, ensuring efficient energy transfer throughout the vehicle.
Termination techniques are specifically engineered to handle the high-current demands of EV motor wiring harness applications, delivering stable and safe performance under fast-charging conditions.
Automation and Scalability
Celestix employs cutting-edge automated EV harness production lines that boost consistency and throughput for high-volume orders.
We offer rapid EV harness prototyping—delivering validated sample units within 1–2 weeks to support accelerated product development cycles.
Our workforce includes IPC-A-620-certified technicians with expertise in hybrid assembly, ensuring that even low-volume or custom harnesses meet top-tier quality benchmarks.
Certifications and Eco-Compliance
All of our harnesses are manufactured to be UL-approved EV harness systems, ensuring compliance with global safety and performance standards.
We are fully certified across RoHS, REACH, ISO 9001, and IATF 16949 protocols, enabling our products to meet regulatory and market entry requirements worldwide.
Our approach to sustainable EV harness solutions includes the use of recyclable materials, eco-conscious packaging, and process efficiency that reduces environmental impact.
Technical Specifications
Voltage Rating: Up to 1000V DC
Current Capacity: Up to 500 Amps
Conductors: Tinned copper, aluminum-copper hybrids
Insulation: XLPE, PVC, Teflon, Silicone (RoHS/REACH compliant)
Shielding: Braided, foil, spiral
Connectors: Over-molded, high-voltage, IP67/IP69K
Temperature Range: -40°C to +150°C
Certifications: IATF 16949, ISO 9001, UL, CE, RoHS, REACH, ISO 6722, IEC 60228, ISO 14001, IPC/WHMA-A-620, J-STD-001
Applications
Battery Management Systems (BMS)
Electric Motors & Inverters
DC Fast-Charging Infrastructure
Vehicle Control Units (VCUs)
HVAC & Thermal Management
ADAS & Autonomous Modules
Charging Ports & Onboard Chargers
Sensor and Infotainment Networks
Why Partner with Celestix?
End-to-end engineering from design to mass production
In-house testing: EMI, mechanical, thermal, and electrical
Agile capacity for pilot, small batch, and large-scale runs
Advanced traceability: barcoding, serialization, and VMI support
Open collaboration with OEM engineering and design teams
Engineered to your specs. Delivered on time. Backed by global standards.
To start your EV wiring project, reach out via our contact form or email our technical sales team.
FAQs
Do your harnesses support 800V systems?
Yes, we design for up to 1000V DC, tested for insulation, safety, and current load.
Do you provide EMI testing and compliance documentation?
Absolutely. Every project includes lab-tested EMI data and global compliance reports.
What’s your prototyping lead time?
1–2 weeks depending on design. Rapid iteration is built into our workflow.
How are Celestix harnesses different?
We combine lightweight materials, robust EMI shielding, over-molding, and compliance to deliver automotive-grade reliability.
Can we collaborate on harness design?
Yes, our engineers offer CAD, simulation, and DFM support. We work closely with your team from start to finish.
About Celestix Industries India Pvt Ltd
Founded in 2010 and rebranded in 2025, Celestix is a leading Indian manufacturer of custom wiring harnesses and injection-molded components. With manufacturing sites in Pune, Ahmedabad, and Greater Noida, we serve global OEMs across the automotive, EV, telecom, defense, and consumer electronics industries.
We are driven by our DRIVE culture:
Dedication to customers
Respect and teamwork
Integrity and accountability
Value and prioritization
Excellence in action
Build the EV future with Celestix—where performance meets precision.