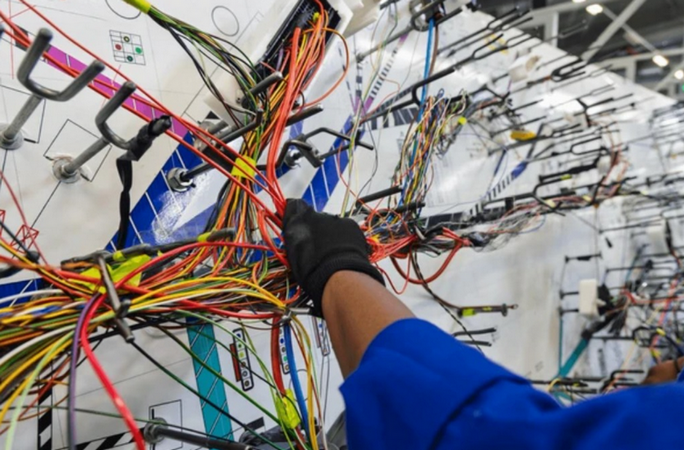
A Step-by-Step Guide to Wiring Harness Manufacturing
When performance and reliability are non-negotiable, a precisely engineered wiring harness becomes mission-critical. At Celestix Industries India Pvt Ltd, we go beyond manufacturing—we collaborate. With over 15 years of hands-on expertise, global certifications, and advanced production capabilities, we’re a trusted contract manufacturer for OEMs and Tier 1 suppliers worldwide.
This guide isn’t just about wires and connectors—it’s a detailed exploration of the wiring harness process that powers modern technology across sectors like automotive, medical, telecom, defense, and consumer appliances. From concept to compliance, our structured approach to custom wiring harness manufacturing ensures accurate integration, consistent performance, and reliable delivery.
In this wire harness guide, we outline each critical phase—prototyping, layout review, wire preparation, crimping, over-molding, rigorous testing, and packaging. Whether you're an engineer focused on specifications or a buyer evaluating suppliers, this comprehensive overview of wire harness manufacturing steps helps you understand what quality and control should look like.
Let’s explore the full wiring harness manufacturing journey—and highlight best practices every OEM should expect.
Step 1: Requirements & Design Collaboration
Every successful wiring harness begins with a thorough understanding of its application, installation environment, and required functionality. Our collaboration with your technical team includes:
Interpreting system schematics, load paths, and interface points
Identifying challenges such as tight routing spaces, EMI zones, or thermal exposure
Choosing terminal types, seals, and insulation materials that suit specific applications (e.g., automotive engine bays vs. medical enclosures)
Confirming electrical load, current carrying capacity, voltage thresholds, and shielding requirements
Our process incorporates early compliance checks to align with standards such as ISO 9001, UL, CE, and customer-specific criteria. We offer:
CAD design validation and 3D routing models (ISO wiring harness guide)
Materials engineering input based on environmental conditions
Prototypes delivered in 1–2 weeks (wire harness prototyping, step-by-step harness prototyping)
All components are finalized with customer approval. No substitutions occur without documented sign-off. That’s core to our contract wiring harness process and long-term trust.
Step 2: Material Sourcing
Using quality-certified components is non-negotiable in wiring harness manufacturing. We source from global leaders to ensure consistent electrical and mechanical performance:
Copper conductors (bare, tinned, plated) compliant with ISO 6722 and IEC 60228
High-grade insulation (PVC, Teflon, silicone) for thermal and chemical resilience
Industry-standard connectors, seals, and terminals from Molex, TE, Amphenol, and others
All materials meet or exceed RoHS, REACH, CE, UL regulations (UL-approved harness manufacturing, BIS-compliant harness guide)
We maintain buffer stocks of common components to support scalable harness production guide strategies and reduce lead times.
Step 3: Wire Cutting, Stripping & Crimping
Precision preparation is critical to long-term harness reliability. Our in-house automated wiring harness production systems include:
High-speed cutters and strippers that meet +/- 0.5 mm tolerance (wire cutting harness guide, stripping wiring harness process)
Laser wire marking for batch traceability
Programmable crimping systems with integrated pull-force and cross-section analysis (crimping wire harness steps)
We support manual wire harness assembly for prototypes and specialized builds. Our QC system ensures that every crimp meets mechanical strength and conductivity requirements. We also utilize ultrasonic welding harness methods where required for splices and junctions.
Step 4: Harness Assembly & Splicing
Wires are organized, routed, and bundled on custom-designed laying boards. This ensures 1:1 fidelity to the approved layout. Features include:
Custom bundling for bend radii, branch take-offs, and fastening zones
EMI/RFI shielding based on signal sensitivity
Structured placement of connectors, inline fuses, relays, and breakout points
Flexible splicing options including ultrasonic welds, heat-shrink solder joints, and crimp splices (splicing wiring harness guide)
Our ability to adapt mid-build ensures agility in managing engineering changes, making us a true partner in manual wire harness assembly.
Step 5: Sleeving, Over-Molding & Connector Assembly
Protection is engineered into every harness:
Over-molded connectors (up to IP67/IP69K) for harsh environments
Heat-shrink tubing, fabric tape, or braided sleeving for abrasion resistance (harness sleeving manufacturing, harness taping process)
Flame-retardant thermoplastics for high-temp assemblies
Our connector assembly harness process follows IPC and CE specs. These layers of ruggedization enhance service life in EVs, industrial robots, and consumer appliances.
Step 6: 100% Quality Testing
Every finished harness undergoes validation in our in-house harness manufacturing lab. Standard testing includes:
Electrical continuity and high-voltage insulation resistance tests
Visual and mechanical inspections per IPC/WHMA-A-620 standards (IPC harness manufacturing steps)
Pull-force testing, crimp micrographs, and shielding continuity
Accelerated life testing (humidity, vibration, thermal cycles)
We document results with every shipment. This is core to our quality control harness manufacturing philosophy.
No harness ships without a signed Certificate of Conformance.
Step 7: Labeling, Packing & Documentation
Final delivery is designed to simplify your logistics and line-side installation:
Color-coded labels, heat-shrink tags, and barcoding for traceability
Harness taping process ensures clean routing and packaging
Units are oriented (LH/RH) for intuitive unpacking
Export-ready packaging: anti-static bags, moisture barriers, and fumigated wooden crates
We include full documentation: test reports, PPAP (if applicable), CoC, and traceability logs. We support VMI, JIT, and consolidated kitting models for OEM wiring harness manufacturing workflows.
Why Engineers & OEMs Choose Celestix
Certified quality systems: ISO 9001:2015, IATF 16949:2016, UL, CE, RoHS, REACH
Production scalability: From low-volume to full-scale manufacturing
Application expertise: EV, HVAC, smart appliances, telecom, automation
End-to-end support: From design review to rapid prototyping to logistics
Custom engineering: Flexible, responsive, and aligned with your specs
We are a long-term partner in reliable wiring harness production, not just a vendor.
Whether you're sourcing for a new product, refining an existing build, or just exploring best practices in wiring harness manufacturing, we hope this guide provided clarity and actionable insights. For further information, data sheets, or process validation templates, feel free to reach out via our contact page or resource center.
FAQs: Your Wiring Harness Questions, Answered
Can you handle complex, multi-branch harnesses with mixed connectors?
Yes. We specialize in high-mix builds across automotive, telecom, and medical sectors. Perfect for custom wiring harness manufacturing needs.
Do you offer design support for customers without finalized harness drawings?
Yes. While we operate as a contract manufacturer, our engineering team collaborates with your designers to suggest alternative components, optimize layouts, and improve manufacturability.
What certifications do your harnesses meet?
All harnesses meet ISO 9001:2015 (Quality Management Systems), IPC/WHMA-A-620 (Acceptability of Cable and Wire Harness Assemblies), IATF 16949:2016 (Automotive Quality Management), as well as RoHS, REACH, and additional global compliance standards.
Do you support urgent/rush builds?
Yes. We support expedited production depending on customer needs and project scope. Our flexible capacity enables us to adapt quickly using scalable harness production guide workflows.
What types of testing do you perform in-house?
We conduct continuity, high-voltage, pull-force, crimp cross-section, thermal, moisture, and vibration testing. All testing is traceable and compliant with customer specs.
Are your products export-ready?
Absolutely. We provide anti-static and moisture-resistant packaging, custom labeling, and export documentation compliant with international shipping regulations.
Can I visit your facility?
Definitely. We welcome client audits and in-person quality checks.
Engineered to your specs. Manufactured for performance. Backed by trust.
Celestix Industries – Your partner in precision wiring solutions. This is the definitive Celestix wiring harness guide.